Silicon Carbide (SiC) Power MOSFETs Address the Needs of Efficient Power Applications
SiC MOSFETs offer a compelling solution for high-efficiency and high-frequency power electronics applications.
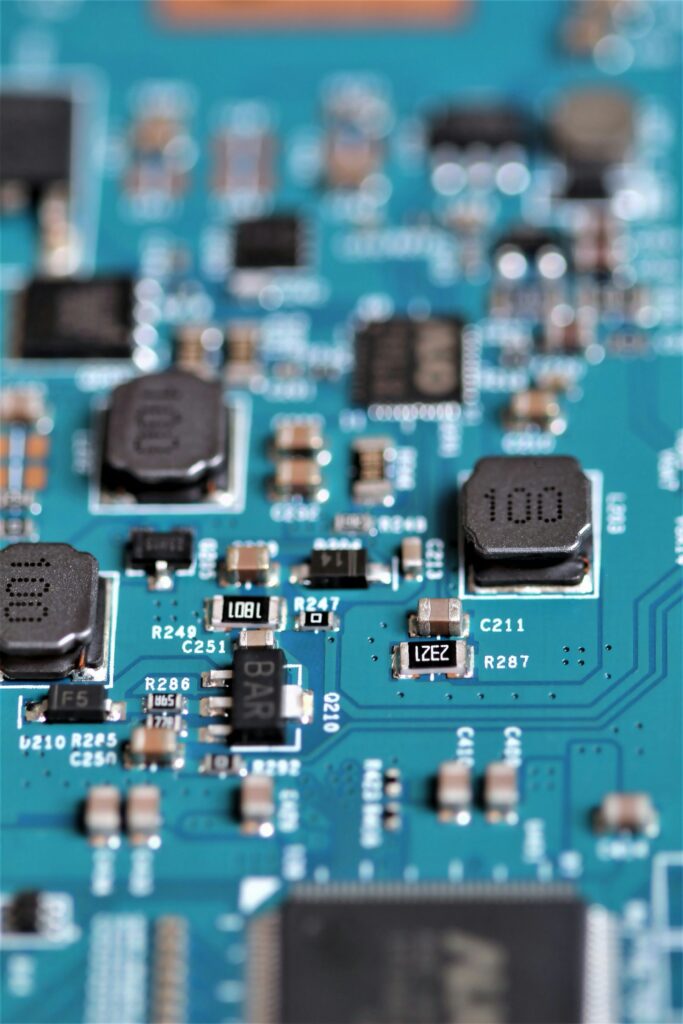
Silicon Carbide (SiC) Power MOSFETs Address the Needs of Efficient Power Applications
Silicon Carbide (SiC) MOSFETs have emerged as a promising technology to address the increasing demand for high-efficiency and high-frequency power electronics applications. Their unique properties make them superior to traditional silicon-based MOSFETs in several key areas.
SiC properties
Silicon carbide (SiC) and other wide bandgap materials are preferred over silicon for numerous reasons. To begin, SiC has a greater bandgap than silicon, with typical values of approximately 3.26 electron volts (eV) for SiC and 1.12 eV for silicon. SiC devices are well-suited for high-power and high-temperature applications due to their larger bandgap, which allows them to operate at greater temperatures without damage or breakdown.
The primary advantage of SiC MOSFETs derives from the silicon carbide material. In comparison to traditional silicon-based semiconductors, SiC is distinguished by its remarkable physical and electrical properties. Silicon carbide possesses a greater bandgap than silicon, enabling it to endure elevated temperatures and voltages. This characteristic minimizes both conduction and switching losses, resulting in enhanced energy efficiency.
Moreover, the robust thermal conductivity of SiC facilitates heat dissipation, enabling the development of lightweight and compact power systems. In power electronics, effective heat management is crucial for the dependability and longevity of devices, making this attribute of utmost significance.
When compared to silicon, the critical parameter of electron mobility in SiC is substantially larger. Faster switching rates in electronic devices are a result of the material’s increased electron mobility, which increases the speed at which charge carriers may travel through it. Since this quality lessens switching and conduction losses, it finds special use in efficiency-critical power electronics applications.
An electric field can accelerate the velocities of electrons (in N-channel MOSFETs) and holes (in P-channel MOSFETs), and the mobilities (μ) of these two channels measure this acceleration. The ratio of the speed to the electric field (E) is the definition of mobility (μ). Elevated electrical conductivity, which results in less resistance, is correlated with increased mobility (μ). “Saturation drift velocity” is the name given to the maximum possible speed.
Electron mobility is a metric that quantifies the rate at which electrons can traverse a material in response to an electric field. This results in a lower on-resistance (RDS(on)) because SiC has a higher electron mobility than Silicon, which allows electrons to traverse the channel more swiftly. Furthermore, the thinner depletion region in the channel is facilitated by the wider bandgap of SiC, which results in a lower on-resistance. This is because electrons can move more readily between the source and drain terminals.
Since SiC MOSFETs exhibit significantly lower on-resistance (RDS(on)) compared to silicon MOSFETs, leading to reduced conduction losses, especially at higher temperatures. This results in improved efficiency, especially in high-power applications.
The on-resistance in MOSFETs is a vital parameter, significantly influencing both power dissipation and the overall efficiency of the device. A decrease in on-resistance results in improved conduction and minimized power losses. Professionals frequently aim to reduce RDS(on) to enhance the functionality of MOSFETs across a range of electronic applications, including power amplifiers, voltage regulators, and switching power supplies.
In addition, SiC has better thermal conductivity than silicon. Compared to silicon, SiC has a thermal conductivity that is around three times greater. SiC devices can function at higher power levels and in more challenging thermal settings thanks to their improved heat dissipation made possible by their increased thermal conductivity. Electronic component longevity and dependability depend heavily on improved thermal performance.
The elevated breakdown electric field strength of SiC devices, frequently surpassing 10 times that of silicon, enables operation at higher voltages, rendering them appropriate for applications that necessitate increased voltage and power levels. SiC MOSFETs can handle higher voltage ratings without increasing the device’s physical size, enabling the design of smaller and more efficient power converters.
SiC MOSFETs have superior switching characteristics, including lower gate charge and faster switching times. This reduces switching losses, especially at high frequencies, further contributing to higher efficiency. As mentioned earlier, the fast-switching speeds of SiC MOSFETs minimize switching losses, allowing for operation at higher frequencies. This enables smaller and lighter power converters with higher power densities. The high-frequency operation and lower conduction losses of SiC MOSFETs generate less heat, simplifying thermal management requirements. This allows for more compact and efficient power systems.
Specific applications
SiC MOSFETs are widely used in many different industries, however, they are most commonly seen in electric power systems and power electronics. Because SiC devices allow for greater power density and efficiency, they find widespread application in power inverters and converters. Small and lightweight power electronic systems made possible by SiC MOSFETs greatly improve the efficiency of renewable energy systems and electric cars (EVs) by increasing the driving range of EVs solar inverters and wind converters, respectively.
On top of that, SiC MOSFETs are great for uses that call for high switching frequencies due to their strong switching capabilities. Power supplies benefit from this because smaller passive components, smaller systems, and better transient responsiveness are the outcomes of higher switching frequencies.
Electric car traction inverters and motor drives benefit from the enhanced efficiency and power density brought about by SiC MOSFETs. These devices can withstand higher operating temperatures, which makes them perfect for the harsh conditions found in automobiles and guarantees dependable and sturdy functioning.
Electric vehicle chargers, uninterruptible power supplies, solar string inverters, and solar optimizers are all possible because of their high efficiency and high voltage operation.
SiC MOSFETs are particularly well-suited for a wide range of applications, including:
- Automotive: Electric vehicles (EVs) and hybrid electric vehicles (HEVs) require high-efficiency power converters for battery charging, motor drives, and auxiliary power systems. SiC MOSFETs can significantly improve the efficiency and power density of these systems.
- Renewable energy: Solar inverters and wind turbine converters benefit from the high efficiency and high-frequency capabilities of SiC MOSFETs, leading to higher energy yields and reduced system costs.
- Industrial power supplies: SiC MOSFETs can enhance the efficiency and power density of industrial power supplies, such as those used in data centers and manufacturing facilities.
- Consumer electronics: SiC MOSFETs can enable smaller, lighter, and more efficient power adapters and chargers for smartphones, laptops, and other electronic devices.
Challenges and future trends
While SiC MOSFET technology is rapidly advancing, there are still challenges to overcome, such as cost and reliability. However, ongoing research and development efforts are addressing these issues, and it is expected that SiC MOSFETs will continue to play a crucial role in shaping the future of power electronics.
In conclusion, SiC MOSFETs offer a compelling solution for high-efficiency and high-frequency power electronics applications. Their superior performance, coupled with ongoing advancements in technology, makes them a promising choice for a wide range of industries.